How tungsten carbide rings are made
If you are in the market for a tungsten wedding band, you may want to understand exactly how these beautiful rings are made. The revolutionary processing of the hardest metal ever used to craft wedding rings involves cutting edge machinery and techniques. By understanding the work behind the magnificent masterpiece, not only could someone appreciate the beauty of it more, a better decision can also be made when choosing the best ring that you will be wearing for the rest of your life.
1. Creating the blank from powder
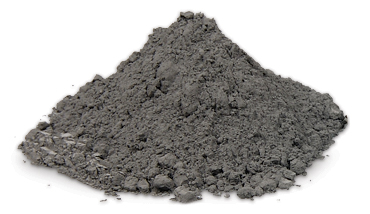
Pure tungsten metal and carbon are ground to fine powder, then the powder is put inside a mold in the shape of the ring that is to be created. The mixture is compressed in the mold and the mold is heat to about 1400 degree Celsius in a vacuum furnace for the tungsten to bind with the carbon to form the tungsten carbide structure, and this patented process is usually referred to as sintering.
2. Polishing the ring blank
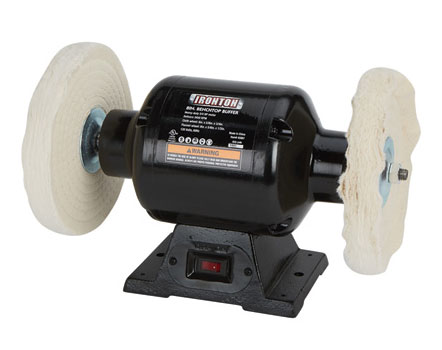
After it is created, the ring blank is a rough and black piece of alloy that will go through about 30 different steps of polishing to achieve the glossy shine that you see in the jewelry store. Most of these polishing are done with a regular polishing machine used for polishing gold and silver jewelry. However, due to the extreme hardness of tungsten carbide, diamond polishing paste is used instead of traditional polishing wax. Diamond polishing paste is the same compound used in diamond polishing. The micron (or grit) of paste used starts from 80 microns and each of the polishing step is reduced to achieve a finer polish. Eventually, a 0.5 micron paste is used to achieve the mirror like high polish finish of most of the tungsten bands.
3. Finishing the ring satin or matte finish
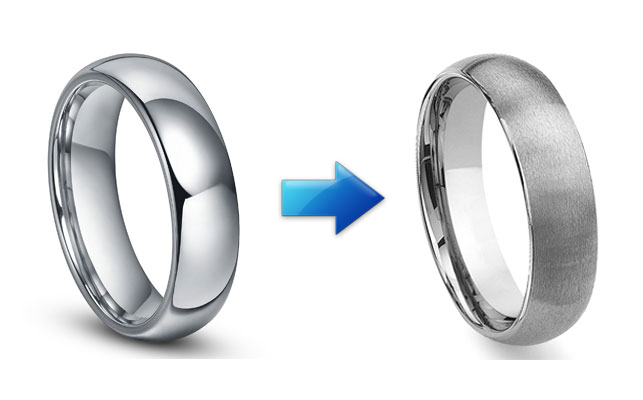
If part of the tungsten ring has a satin, brushed or matte finish, the ring will go through another finishing process in which diamond coated wheels or discs are used. With a 9.5 hardness on the Mohs scale, only diamond coated tools can be used to scuff the surface to create the brush look.
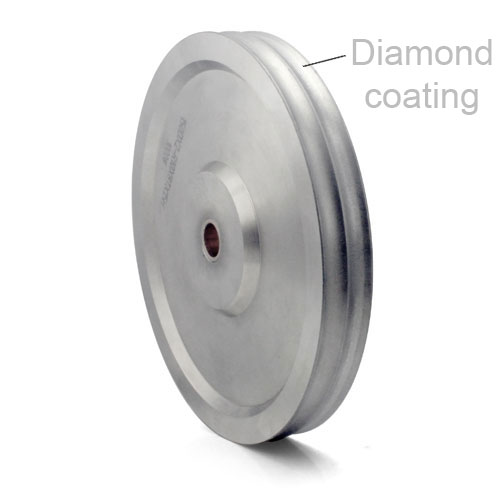
When brush finishing a rounded surface, a diamond coated wheel is used with a regular polishing machine.
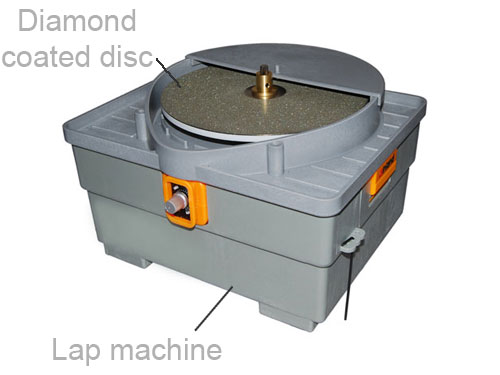
A diamond coated discs with a lap machine is used instead when finishing a ring with flat surface.
4a. Setting diamonds or other precious stones
A high power laser machine is used to cut holes in a tungsten ring where gemstones are to be set. This requires extremely high power laser and high accuracy. Since tungsten carbide is non-malleable, the dimensions of the opening created has to be the exact size of the diamond setting (or housing). Otherwise, it will either not fit or it will fall out very easily.
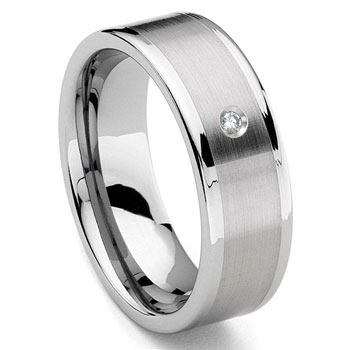
After the hole is cut, the diamond is then placed into the ring and a stainless steel setting is placed on top to secure the stone in place.
NOTE: Some jewelers might tell you that tungsten carbide is indestructible, but the truth is that it is not. Tungsten rings could fracture, especially after a tungsten ring is cut to create the diamond settings. The openings become "weak points" because the ring is much thinner due to the cutting. These are the spots that could fracture upon impact. See the illustration the cross section of a tungsten ring with a diamond setting. So if you are going to activities that involve impacts, such as playing baseball, try to take the ring off to avoid damage.
4b. Setting inlay on blanks
Some blanks are created with grooves for setting inlays. The choices for inlays include silver, gold, platinum, wood, stones, carbon fiber and ceramic.
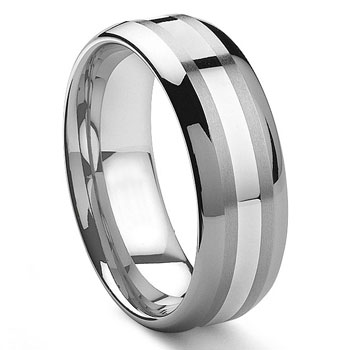
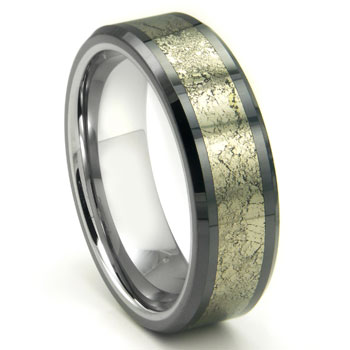
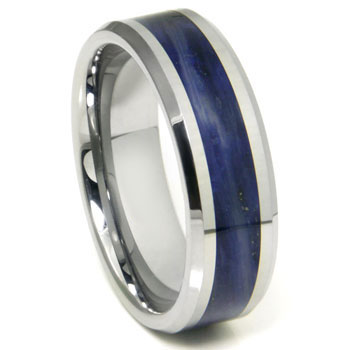
NOTE: Although tungsten rings are very strong and virtually scratch proof, the inlays on them are not. Precious metals such as silver, gold and platinum are very soft, and the inlays created from these metals will sustain the same level of scratching as if you were wearing a silver, gold or platinum ring alone. Although the tungsten part does provide some support and protection on the sides, a gold inlay will scratch just like a gold ring. Take the ring off when working with your hands will keep the inlay from being scratched by hard objects such as hand tools or steel handles.
4c. Laser engraving designs
Some tungsten rings are created by putting designs or patterns on plain tungsten rings. A lower power laser machine is used to engrave the designs. The engraving created this way is crisp and permanent.
Related Topics: